What is DFA?
Design for Assembly (DFA) is a methodology aimed at reducing manufacturing costs by simplifying product structures and assembly processes. It prioritizes ease of assembly, aiming to minimize the number of assembly operations and ensure that the assembly process is as efficient, error-free, and cost-effective as possible. This is achieved by reducing the number of parts in a product, designing parts that are easy to handle and insert, and minimizing the need for fasteners and tools.
DFA was first formalized as a methodology by Dr. Geoffrey Boothroyd and Dr. Peter Dewhurst in the early 1980s. Their research at the University of Rhode Island led to the development of a systematic approach to simplifying product designs for assembly. Their method involved quantifying assembly efficiency and providing guidelines on how to redesign products to reduce assembly costs.
In this article we’ll be reviewing some of the key principles outlined by Boothroyd and Dewhurst, so that we can put together a concise and well informed list of DFA best practices for mechical engineers and product developers. We won’t be covering the methodology in depth, but will borrow from it extensively.
Why DFA?
Some experts estimate that 80% of product cost is determed during design. Regardless of the exact amount, it’s a fairly safe assumption that the majority of a product’s cost is locked at the design stage. Because assembly complexity is a direct function of design choices, applying design for assembly principles early during design has a fantastic return on investment.
Applying Design for Assembly (DFA)
The DFA methodology rests on a central belief: the simpler a product is to assemble, the lower its production costs will be. By focusing on reducing the number of parts and optimizing those that remain for ease of handling, feeding, and insertion, assembly becomes more straightforward and less expensive.
Core DFA principles
These are the core DFA principles outlined by Boothroyd and Dewhurst, as well as other DFA methodologies. We’ll be taking a look at each principle in depth in the following section.
- Reduce part count.
- Modularize and standardize.
- Simplify product structure.
- Reduce assembly time.
- Mistake proofing.
Reduce part count
In this fantastic off the cuff interview on Everyday Astronaut, Elon Musk says “…possibly the most common error of a smart engineer, is to optimize a thing which should not exist.” This highlights the first and most basic DFA principle, reducing part count. The Boothroyd Dewhurst method outlines a formal process of functional analysis for determining the necessity of individual components. We won’t cover this method in depth, but we can highlight the key questions you should be asking below:
-
For each component, ask yourself “is this part necessary at all?” Many times components are included ‘just in case’ during development, and then are never deleted from the final product. This is the first and simplest check.
-
Can a part’s primary function be performed by another part already in the assembly (with or without modifications)?
-
Can multiple parts be combined into a single part? Oftentimes, a singificantly more complex, but monolithic component can eliminate a huge number of assembly steps by accepting a slightly higher production cost for the part. Tesla has done a fantastic job of this by using a small number of large castings to construct vehicle chassis, instead of multiple welded sheet structures.
Modularize and standardize
If the net number of parts (instances) cannot be reduced, modularizing and standardizing around a reduced number of unique parts can help to reduce assembly cost and prevent mistakes. The classic example of this approach is to standardize around a few fasteners. This reduces the number of tools required during assembly, and reduces the likelihood of improper fastener installation.
The same principle applies at the custom part level. One simple approach is to aim for multi-function or multi-purpose parts. For example, in an assembly with two custom brackets designed to hold down other components, instead of designing separate brackets, see if the two brackets can be merged into one part. Look for orthogonal functionality and geometries that can be easily combined without functional loss or significant complexity.
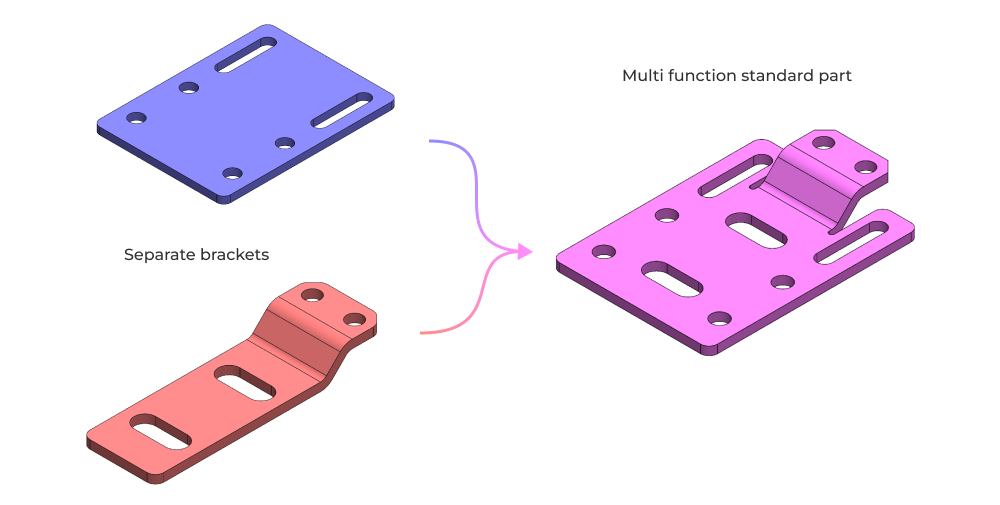
Simplify product structure
Assembly cost is a direct function of product structure complexity. A key principle of DFA is to simplify product structure by designing parts that are both self locating and self fastening.
-
Self-Locating Parts: Design components that inherently guide themselves into the correct position during assembly, minimizing the need for additional tools or fixtures. ex: tab and slot keyed features for component relative positioning without an external fixture.
-
Self-Fastening Parts: Use parts that can secure themselves without the need for additional fasteners. Snap-fits, press-fits, and tab-slot designs can eliminate screws, bolts, and other separate fasteners.
Reduce assembly time
Most components are still assembled manually or semi-manually with hand operated tools. There are obvious exceptions to this, but the basic principles still apply for reducing assembly time. Boothroyd and Dewhurst focus on part handling and part insertion as the primary drivers of assembly time. Here are the key takeaways for each:
Part handling:
-
Design parts that have end-to-end symmetry and rotational symmetry about the axis of insertion. If this cannot be achieved, try to design parts having the maximum possible symmetry.
-
Design parts that, in those instances where the part cannot be made symmetric, are obviously asymmetric.
-
Provide features that will prevent jamming of parts that tend to nest or stack when stored in bulk.
-
Avoid features that will allow tangling of parts when stored in bulk.
-
Avoid parts that stick together or are slippery, delicate, flexible, very small, or very large or that are hazardous to the handler (i.e., parts that are sharp, splinter easily, etc.)
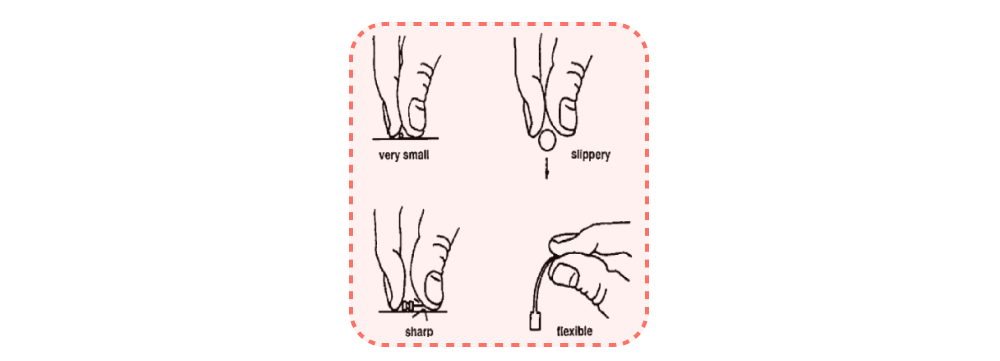
-
In general, choose geometries that are easier to handle, or design in affordances for assembly.
Part insertion:
-
Design so that there is little or no resistance to insertion and provide chamfers to guide insertion of two mating parts. Generous clearance should be provided, but care must be taken to avoid clearances that will result in a tendency for parts to jam or hang-up during insertion.
-
Standardize by using common parts, processes, and methods across all models and even across product lines to permit the use of higher volume processes that normally result in lower product cost.
-
Use pyramid assembly - provide for progressive assembly about one axis of reference. In general, it is best to assemble from above.
-
Avoid, where possible, the necessity for holding parts down to maintain their orientation during manipulation of the subassembly or during the placement of another part. If holding down is required, then try to design so that the part is secured as soon as possible after it has been inserted.
-
Design so that a part is located before it is released. A potential source of problems arises from a part being placed where, due to design constraints, it must be released before it is positively located in the assembly. Under these circumstances, reliance is placed on the trajectory of the part being sufficiently repeatable to locate it consistently.
-
When common mechanical fasteners are used the following sequence indicates the relative cost of different fastening processes, listed in order of increasing manual assembly cost.
- a. Snap fitting b. Plastic bending c. Riveting d. Screw fastening
-
Avoid the need to reposition the partially completed assembly in the fixture.
Mistake proofing (poka-yoke)
Mistake proofing should be seen as an extension of product structure simplification with an eye towards preventing assembly errors that are common to fast moving operations. One common mistake is orienting components incorrectly during assembly, most often a result of partial symmetry that allows multiple assembly orientations. Poka yoke is a design technique that uses asymmetry to enforce compatible assembly configuration and eliminate incompatible configurations.
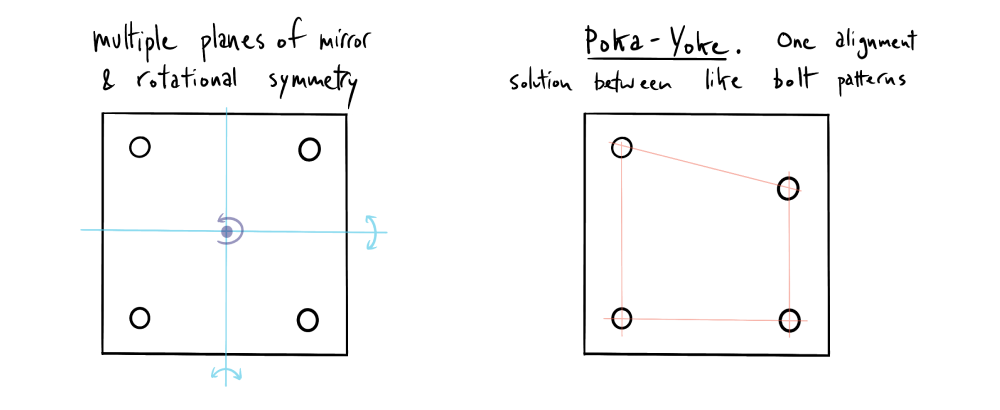
Fold DFA into your continuous design review practice
All of these DFA principles are useless unless you apply them with consistency and frequency during your design process. Along with DFM reviews at the part level, DFA principles should be folded into a regular and continuous design review practice that all engineers follow. Five Flute is built to help teams apply this level of engineering rigor without heavy weight process overhead. It’s the easiest way to share, review, markup, and improve your engineering designs.
If you want an easy way to run DFA reviews with your team, check out Five Flute.
Related articles
Fasteners and bolted joint design